Differences Between Ball Bearings, Sleeve Bearings, Hydrostatic Bearings, and Magnetic Bearings
Bearings are crucial components in machinery, widely used to support rotating parts and reduce friction. Depending on the specific needs of the application, different types of bearings offer varying load capacities, speeds, and operational characteristics. In this comprehensive guide, we will explore the key differences between ball bearings, sleeve bearings, hydrostatic bearings, and magnetic bearings, focusing on their advantages, disadvantages, and ideal use cases.

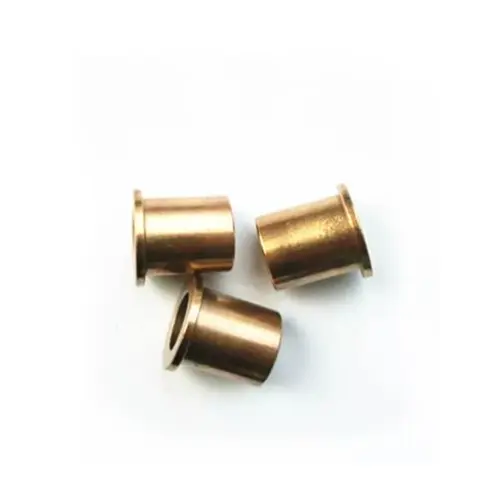
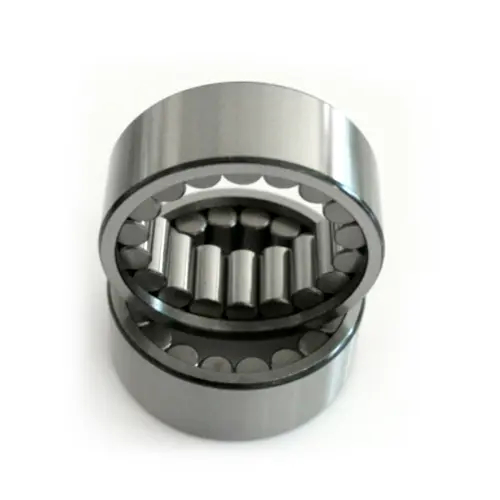
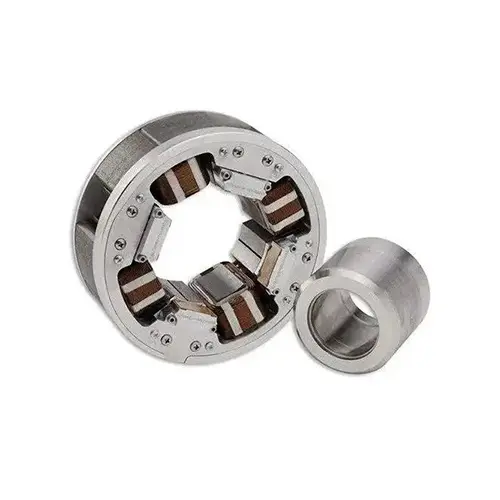
1. Ball Bearings: High-Speed, Low-Friction Solution Principle & Structure:
Ball bearings are one of the most commonly used bearing types. They feature rolling elements (typically steel or ceramic balls) that rotate between an inner and outer race to carry load. The rolling motion significantly reduces friction, making them ideal for high-speed applications.
Advantages of Ball Bearings:
- Low Friction: The rolling contact results in minimal friction, enhancing efficiency for high-speed machinery.
- High Precision: Ball bearings offer excellent precision and smooth operation, making them ideal for applications requiring high accuracy.
- Versatile Applications: Ball bearings are widely used in small electric motors, household appliances, automotive components, and more.
Disadvantages of Ball Bearings:
- Limited Load Capacity: While ideal for moderate loads, ball bearings have lower load-bearing capacities compared to other bearing types.
- Susceptibility to Contamination: Dust, dirt, and other contaminants can reduce the performance and lifespan of ball bearings.
Common Applications:
- Electric Motors
- Fans
- Home Appliances
- Automotive Wheels
2. Sleeve Bearings: Cost-Effective for Heavy Loads
Principle & Structure:
Sleeve bearings, also known as plain bearings or journal bearings, use a sliding contact between the shaft and the bearing material (usually metal or composite). Lubrication is critical for reducing friction and preventing wear.
Advantages of Sleeve Bearings:
- High Load Capacity: Sleeve bearings are excellent for heavy-load applications, especially in low-speed environments.
- Simple Design: With fewer moving parts, sleeve bearings are easy to design, manufacture, and maintain.
- Low Noise: The absence of rolling components results in quieter operation compared to ball bearings.
Disadvantages of Sleeve Bearings:
- Higher Starting Friction: Sleeve bearings typically have higher friction at startup, requiring sufficient lubrication.
- Unsuitable for High Speeds: Due to the sliding motion, sleeve bearings are less effective in high-speed applications.
Common Applications:
- Electric Motors
- Gearboxes
- Fans
- Industrial Machinery
3. Hydrostatic Bearings: High-Load, Low-Friction Performance
Principle & Structure:
Hydrostatic bearings use pressurized fluid (usually oil) to form a thin film that supports the shaft. An external pump keeps the fluid under pressure, preventing direct contact between the shaft and the bearing surfaces, resulting in virtually no friction.
Advantages of Hydrostatic Bearings:
- Extremely High Load Capacity: Hydrostatic bearings can support massive loads, making them ideal for heavy-duty and high-performance applications.
- Zero Friction: The fluid film minimizes friction, improving efficiency and performance.
- Stable Operation: These bearings provide stable, vibration-free operation, making them ideal for precision equipment.
Disadvantages of Hydrostatic Bearings:
- Complex Design: The system requires pumps, valves, and a dedicated fluid reservoir, making it more complex to design and maintain.
- Fluid Dependency: Hydrostatic bearings require specific fluids, which need regular monitoring and replacement.
Common Applications:
- Heavy Industrial Machinery
- Turbines
- Compressors
- Marine Engines
4. Magnetic Bearings: Frictionless and High-Speed Performance
Principle & Structure:
Magnetic bearings use electromagnets or permanent magnets to support a rotating shaft without physical contact. Magnetic fields are dynamically adjusted to maintain the position of the shaft, essentially levitating it.
Advantages of Magnetic Bearings:
- Zero Friction: Magnetic bearings eliminate all mechanical friction, offering unmatched efficiency and minimal wear.
- Precision & Stability: These bearings provide ultra-precise control over the shaft position, making them ideal for high-speed, high-precision machinery.
- Extended Lifespan: Without physical contact, magnetic bearings experience virtually no wear, resulting in a longer operational lifespan.
Disadvantages of Magnetic Bearings:
- High Cost: The complex design, along with the need for electromagnetic controls, makes magnetic bearings more expensive.
- Temperature Sensitivity: Magnetic bearings can be sensitive to temperature fluctuations, requiring advanced thermal management systems.
Common Applications:
- High-Speed Turbines
- Medical Devices
- Aerospace Equipment
- Flywheels
Comparison of Bearing Types
Bearing Type | Load Capacity | Speed | Advantages | Disadvantages | Typical Applications |
---|---|---|---|---|---|
Ball Bearings | Moderate | High Speed | Low friction, high precision, versatile | Limited load capacity, sensitive to contamination | Motors, fans, appliances, automotive |
Sleeve Bearings | High | Low Speed | High load capacity, simple design, quiet | Higher starting friction, unsuitable for high speeds | Motors, gearboxes, industrial machinery |
Hydrostatic Bearings | Very High | Low to Moderate | Extremely high load capacity, zero friction | Complex design, fluid dependency | Heavy machinery, turbines, compressors |
Magnetic Bearings | Very High | Very High Speed | Frictionless, high precision, long lifespan | High cost, temperature sensitivity | Turbines, medical devices, aerospace |
Conclusion: Choosing the Right Bearing for Your Needs
Each type of bearing has distinct advantages suited to specific applications.
- Ball bearings are perfect for high-speed, moderate-load scenarios where efficiency and precision are key.
- Sleeve bearings offer a simple and cost-effective solution for heavy-load, low-speed operations.
- Hydrostatic bearings excel in heavy-duty, high-performance environments where minimal friction is essential.
- Magnetic bearings provide frictionless, ultra-high-speed performance for high-precision applications in advanced machinery.
About HDHFAN
HDHFAN is a leading cooling fan manufacturer specializing in high-quality DC cooling fans, metal AC fans, silent blowers, PWM speed controlled axial fans, waterproof cooling fans, CPU coolers and cross flow fans. If you are equally committed to quality in your products, we sincerely invite you to contact us. Our high-performance fans will provide you with the best solutions, ensuring your satisfaction and reliability.